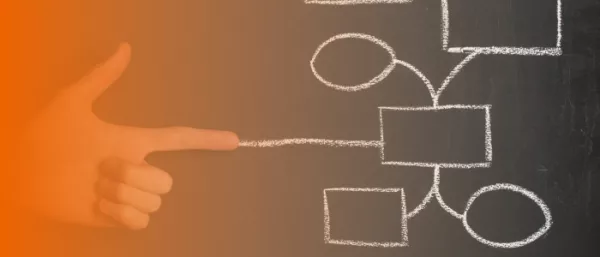
Save costs and increase efficiency through process orchestration
How can companies increase efficiency and cut costs in an uncertain economic environment?
Moreby Veronika Altenbach
Effiziente Prozesse sind das Herzstück eines erfolgreichen Unternehmens. Doch viele Organisationen kämpfen mit Engpässen, ineffizienten Abläufen und unnötigen Kosten. Wie lassen sich diese Herausforderungen meistern? In diesem Artikel zeigen wir Ihnen, wie Sie in drei Schritten Ihre Prozesse optimieren und welche Methoden wie Lean und Six Sigma dabei helfen. Zudem stellen wir Ihnen eine praktische Checkliste zur Prozessverbesserung zur Verfügung.
Before optimizing your processes, you should consider the most common mistakes so that you can avoid them, such as:
Missing or insufficient process documentation
Solution: Document and standardize processes for greater clarity and consistency.
Inadequate analysis and planning
Solution: Analyze and model processes thoroughly before making any changes.
Lack of automation and digitization
Solution: Systematically check where automation makes sense.
No continuous improvement
Solution: Integrate process improvement as an integral part of your corporate culture.
Lack of employee involvement
Solution: Early communication and active involvement promote acceptance and commitment.
Lack of resource planning
Solution: Plan personnel deployment strategically and flexibly.
Overlooking process deficiencies
Solution: Implement a system for identifying and eliminating process deficiencies.
Lean management and Six Sigma are two proven methods for process optimization. Both approaches help reduce waste and improve quality.
Learn more about these two methods in our Knowledge Hub.
Process optimization is not a one-time project, but a continuous improvement process. Through structured analysis, targeted optimization, and sustainable control, companies can significantly increase their efficiency. Use proven methods and avoid typical mistakes – this is how you can move from bottlenecks to efficiency!
How can companies increase efficiency and cut costs in an uncertain economic environment?
MoreBPM standards are the foundation for a successful digital transformation. Find out how you can use BPMN 2.0 and DMN to optimize your processes and strengthen your competitiveness.
MoreLooking to streamline your business processes? Not every process is suitable for automation. We'll show you how to easily identify the processes that are best suited for automation.