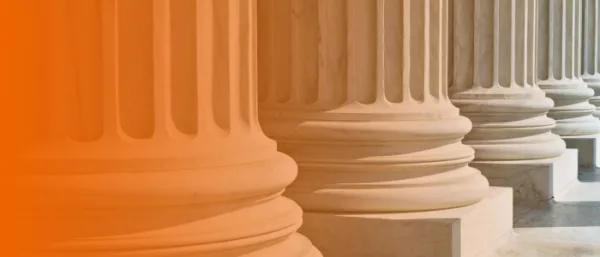
The 5 pillars of process management
Are your business processes up-to-date? Learn how to optimize your operations, boost efficiency, and drive business growth with the five pillars of process management.
by Veronika Altenbach
Inefficient processes are one of the biggest challenges for companies, despite advanced digitalization. They cause high costs, long throughput times, and dissatisfied customers. Despite many attempts at optimization, many companies are unable to improve their processes in the long term. But why is it that some companies stagnate in their processes while others celebrate success?
In this article, we show you how companies can effectively design and improve their processes. We not only highlight the most common stumbling blocks and success factors, but also present strategic approaches that will help you optimize your process management in the long term.
Many companies struggle with inefficient processes that lead to high costs, long throughput times, and dissatisfied customers. Typical challenges include:
Now that we have looked at the most common challenges in process management, let's take a look at what successful companies have in common:
A well-thought-out process management strategy is essential to maximize your company's chances of success. Below, we have compiled five key steps to help you optimize your processes in a targeted manner:
Successful process management is based on clear strategies, technological progress, and a culture of continuous improvement. Companies that control their processes in a targeted manner, make data-based decisions, and actively involve their employees in change increase their efficiency and competitiveness in the long term. If you follow the five steps presented here, you will be a big step closer to successful implementation than many other companies.
Are your business processes up-to-date? Learn how to optimize your operations, boost efficiency, and drive business growth with the five pillars of process management.
The key to success in today's business world is well-structured process management in order to increase service quality and stand out from the competition. Find out how efficient processes make the difference.
MoreFind out who is involved in efficient business processes besides process managers and IT professionals, and how they work together to ensure flawless processes.
More